Tuesday Feb 28, 2012 9:36 am
Driverless Trains and the ‘Mine of the Future’: Are Workers Becoming Obsolete?
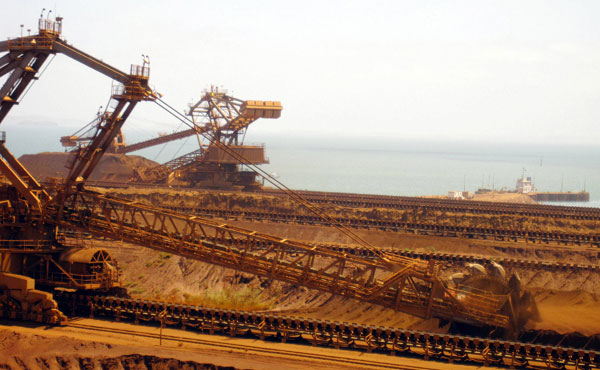
Remote controlled stackers and reclaimers moving iron ore at Rio Tinto's Port Dampier operations in western Australia's Pilbara region in March 2010. (Photo Amy Coopes/AFP/Getty Images)
In a futuristic scenario decried by labor leaders and mining opponents, trains hauling iron ore across vast stretches of Australia’s Pilbara region will by 2014 be operating without drivers. It’s part of the mining giant Rio Tinto’s “Mine of the Future” program, which also includes driverless trucks, autonomous drills and other remote-controlled or robotic equipment replacing manpower.
The company recently announced it is reviving plans put on hold during the economic crisis and investing $518 million in the driverless iron ore trains, which along Rio Tinto’s 1,500-kilometer network will be the world’s first automated long-distance train system. Rio Tinto also reportedly recently bought 150 driverless dump trucks for Pilbara mines. Rio Tinto chief executive Sam Walsh was quoted saying the trains will help the company deal with a shortage of skilled workers. About 500 train drivers will lose their jobs, though Rio Tinto has said they will be retrained for other positions.
The Sydney Morning Herald quoted Construction, Forestry, Mining and Energy Union leader Gary Wood saying that even if those drivers keep their jobs, in the long run automation will mean serious job losses—especially if or when the demand for building materials chills:
Opponents of proposed new Rio Tinto projects in the United States think the “Mine of the Future” project means locals should not believe promises of well-paying jobs. In Superior, Ariz., where Rio Tinto is trying to open a massive new copper mine, during a reporting trip last fall many local residents pointed to company materials touting the Mine of the Future and said they feared that robots, not humans, would be doing many of the jobs if the mine opens.
Rio Tinto’s Mine of the Future website mentions the Resolution Copper project in Arizona as a place where automated boring equipment would facilitate the digging of extremely deep shafts and tunnels needed for the “block cave” method they plan to use. A Resolution Copper spokesman said the Mine of the Future is specific to Australia, and that the proposed Resolution Copper mine would bring many jobs to Arizona.
Automated driverless locomotives are already common inside rail yards in the U.S., a major point of contention for workers and union leaders, who say these locomotives not only cut out union jobs but endanger union workers in the rail yards. They point to a number of rail yard fatalities and injuries where automated locomotives were in operation. (On the flip side, a lawsuit filed on behalf of injured passengers and railroad employees alleges BNSF and Metrolink were negligent in not investing in an automatic braking system that attorneys say could have avoided a fatal 2002 head-on crash.)
It is unclear whether Rio Tinto’s driverless trains are seen as a safety risk in Australia. Much of the territory they will be crossing is desolate. Some miners see automated machinery in mines or on open pit mine sites as an occupational safety risk. But automation can also replace or reduce the need for human workers in some dangerous tasks and areas, proponents say.
Rio Tinto’s website says the Mine of the Future:
Automation has of course played a central role in reshaping manufacturing over past decades, leading to more efficiency, lower prices and job losses in countless industries. But automation of massive tasks like extracting tons of ore a mile below the ground and shipping it cross-country still seems mind-boggling and alternately awe-inspiring or threatening to many people.
A large Utah copper mine run by Rio Tinto subsidiary Kennecott is slated for several new automated systems, including using sensitive machines to sort valuable minerals from waste rock and using automated tunnel-boring machines.
At the Kennecott site, Rio Tinto is partnering with a Norwegian company called TOMRA that specializes in using sensors for automated recycling and food processing and a British company called e2V to develop sorting machines, which will use radio waves and microwaves to instantaneously decide which ore has enough copper to be worth recovering. It is not clear whether job losses due to automation are expected at the Utah mine.
A Reuters story about Rio Tinto’s Australian operations says:
The company recently announced it is reviving plans put on hold during the economic crisis and investing $518 million in the driverless iron ore trains, which along Rio Tinto’s 1,500-kilometer network will be the world’s first automated long-distance train system. Rio Tinto also reportedly recently bought 150 driverless dump trucks for Pilbara mines. Rio Tinto chief executive Sam Walsh was quoted saying the trains will help the company deal with a shortage of skilled workers. About 500 train drivers will lose their jobs, though Rio Tinto has said they will be retrained for other positions.
The Sydney Morning Herald quoted Construction, Forestry, Mining and Energy Union leader Gary Wood saying that even if those drivers keep their jobs, in the long run automation will mean serious job losses—especially if or when the demand for building materials chills:
People talk about reskilling but you don't need a team of truck drivers to sit and operate one computer…Without a strong demand for iron ore there will be a definite loss of jobs … Over ten or twenty years we are going to see a significant demise of these lesser skilled job opportunities.Wood says he expects battles over automation to push nonunion Rio Tinto workers to unionize. In June, Rio Tinto train drivers for the first time won the right to collective bargaining.
Opponents of proposed new Rio Tinto projects in the United States think the “Mine of the Future” project means locals should not believe promises of well-paying jobs. In Superior, Ariz., where Rio Tinto is trying to open a massive new copper mine, during a reporting trip last fall many local residents pointed to company materials touting the Mine of the Future and said they feared that robots, not humans, would be doing many of the jobs if the mine opens.
Rio Tinto’s Mine of the Future website mentions the Resolution Copper project in Arizona as a place where automated boring equipment would facilitate the digging of extremely deep shafts and tunnels needed for the “block cave” method they plan to use. A Resolution Copper spokesman said the Mine of the Future is specific to Australia, and that the proposed Resolution Copper mine would bring many jobs to Arizona.
Automated driverless locomotives are already common inside rail yards in the U.S., a major point of contention for workers and union leaders, who say these locomotives not only cut out union jobs but endanger union workers in the rail yards. They point to a number of rail yard fatalities and injuries where automated locomotives were in operation. (On the flip side, a lawsuit filed on behalf of injured passengers and railroad employees alleges BNSF and Metrolink were negligent in not investing in an automatic braking system that attorneys say could have avoided a fatal 2002 head-on crash.)
It is unclear whether Rio Tinto’s driverless trains are seen as a safety risk in Australia. Much of the territory they will be crossing is desolate. Some miners see automated machinery in mines or on open pit mine sites as an occupational safety risk. But automation can also replace or reduce the need for human workers in some dangerous tasks and areas, proponents say.
Rio Tinto’s website says the Mine of the Future:
…is designed to create next generation technologies for mining operations that result in greater efficiency, lower production costs, improved health, safety and environmental performance, and more attractive working conditions.
Automation has of course played a central role in reshaping manufacturing over past decades, leading to more efficiency, lower prices and job losses in countless industries. But automation of massive tasks like extracting tons of ore a mile below the ground and shipping it cross-country still seems mind-boggling and alternately awe-inspiring or threatening to many people.
A large Utah copper mine run by Rio Tinto subsidiary Kennecott is slated for several new automated systems, including using sensitive machines to sort valuable minerals from waste rock and using automated tunnel-boring machines.
At the Kennecott site, Rio Tinto is partnering with a Norwegian company called TOMRA that specializes in using sensors for automated recycling and food processing and a British company called e2V to develop sorting machines, which will use radio waves and microwaves to instantaneously decide which ore has enough copper to be worth recovering. It is not clear whether job losses due to automation are expected at the Utah mine.
A Reuters story about Rio Tinto’s Australian operations says:
Rio Tinto says it wants to avoid forcing workers to toil beneath the scorching heat of the Pilbara, but automation also enables it to overcome a shortage of skilled labour. The shortage has been fuelled by a boom in mining and energy investment, with $230bn worth of projects under way or approved in Australia. Salaries have sky-rocketed to the point where a truck driver can earn more than $100,000 a year.
At least half of Rio Tinto’s 500 train drivers may lose their current jobs, with the rest to be used on about a fifth of the network that will still need drivers. But the company said no one would be laid off as it aimed to retrain workers for new roles. Trade unions oppose automation, but their influence in the Pilbara has waned as Rio Tinto and rivals such as BHP Billiton have switched to contract labour.